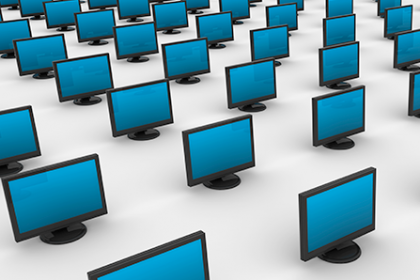
Recently, a manufacturer approached PMC Polymer Products needing help with a specialty compound for a large injection-molded part requiring IR HIPS (Ignition Resistant High Impact Polystyrene).
This part’s complex design made it difficult to mold, and color consistency – an absolute requirement for the application – was an issue. Unacceptable splay repeatedly resulted in a high reject rate, and nothing the molder did to optimize molding conditions would improve yield to a satisfactory level.
After visiting with the customer and molder to observe the issues first-hand and better understand their manufacturing process, PMC scientists offered recommendations to further optimize molding. We never suggest changes to product formulations before attempting simpler solutions.
In this case, molding wasn’t the issue. The reject rate was still too high for our customer.
At that point, it was back to the literal drawing board, as PMC’s expert compounders took the problem into the lab to find a solution through reformulating the compound. A designed lab experiment of base resins resulted in a series of formulations that provided a matrix of varying compound mold-ability and part properties. From there, we identified the best formulation, based on our customer’s performance criteria.
PMC Polymer Products provided a production-scale 1,000-pound sample for the customer to evaluate. The molding trial was a complete success, and the new custom formulation, based on our Avantra® line of IR HIPS, enabled our customer to mold complex parts that meet the performance, quality and cost standards they require.